Our Solutions
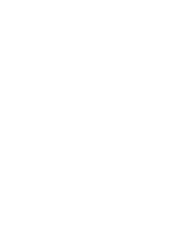
Productivity & Performance Review
Reviewing all aspects of the manufacturing process to perform at optimal performance.
read more
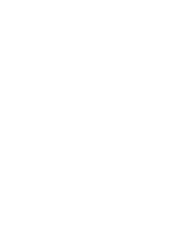
Operational Excellence Review
A department focused process driven review giving insights on performance & productivity.
read more
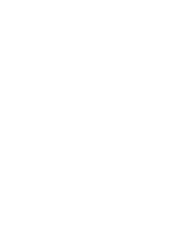
Workplace Review
Understanding the organisation’s goals and current workplace performance – then turning insights into action.
read more
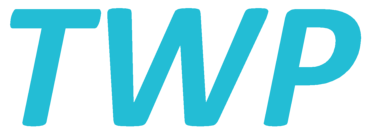
Transformational Work Practices
Clear, practical strategies to improve individual, team and organisational performance.
read more
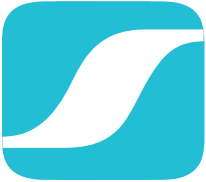
esCollate
Providing real-time data capture and feedback, streamlining processes and engaging factory employees.
read more
Our Approach
The acquisition of knowledge alone does not deliver value to the organisation. Improvement in performance requires behaviour change. Value is realised when people do things differently.
Human-Social factors influence behaviour and ultimately the contribution that an individual makes to the organisation.
An individual’s contribution is not only influenced by their capability but by their motivation, focus of attention and disposition towards both co-workers and the organisation.
Tima Consulting understands the human-social factors that influence an individual’s performance and the approach that can be applied to optimise individual and team outcomes.
Understanding human-social factors and their application leads to improved individual and team performance in areas such as:
- the degree and style of motivation
- preparedness to ’emotional risk’
- preparedness to assist other team members
- minimisation of ‘social loafing’.
The successful application of human-social factors facilitates the development of a performance and learning environment. This in turn leads to individuals and teams that are more accepting of change, are prepared to invest to improve performance and are engaged in achieving organisational goals.
Productivity & Performance Review
Tima is offering a Manufacturing Productivity & Performance
Review and Management Service. This is a process driven review
providing insights impacting Manufacturing Process,
Productivity & Performance.
Our Manufacturing Process, Productivity & Performance Review entails
reviewing all aspects of the manufacturing process including supply chain and it’s people, to ensure that whatever the products that the company is manufacturing is at optimal productivity, that they have the right people, the right strategy and the right tools to perform and through our extensive experience and networks we will assist with rectifying the identified needs.
Our globally seasoned executives who are GM’s, Manufacturing Managers,
Factory Managers, Production Managers, NPD, CI, Engineering, Supply Chain,
Marketing, Sales, IT & CFO’s to solve your Manufacturing Process, Productivity
& Performance issues.
Operational Excellence Review
Tima’s Operational Excellence Review is a department
focused process driven review that will give you a base line
of insights impacting on performance & productivity.
Our seasoned executives with seasoned global experience to solve your; Production, CI, Supply Chain, Logistics & Warehousing (incl Inventory Management), Engineering, Site Management, People Motivation and Engagement.
We can help you & your team by providing; training, coaching, &
applied methods of manufacturing excellence, business transformation, operational excellence, business & continuous improvement, resource planning, as well as plant optimisation modelling, performance management, revenue enhancement, cost reductions or to get your projects back on track.
It is best practice to undertake a review periodically or when key staff leave. Other reasons for doing a review;
– morale falling, staff tension & conflict or high staff turnover.
– reject rates are up, failing quality audits, low productivity or not meeting KPI’s.
Workplace Review
The purpose of a Tima Workplace Review is to establish your
current workplace environment, the relevant workplace history
and strategy to improve the workplace dynamics.
The workplace review involves face to face, structured interviews with small groups spanning the workplace. It is this personal and direct approach that allows the review to penetrate beyond the limits of conventional surveys and to get to the heart of the workplace dynamics.
The approach taken allows the delivery team to demonstrate their understanding and empathy with employees, facilitating both the employees’ openness in communicating workplace issues and gaining their support for the proposed esCollate implementation and change programme.
Following the initial interviews a workshop is conducted where a Workplace Review report documenting key observations is presented and discussed.
Transformational Work Practices – TWP
An effective approach that delivers clear, practical strategies for improving individual, team and organisational performance.
The Transformational Work Practices (TWP) programme provides leaders with the insight, communication skills and strategies they need to effectively manage the transformation of work teams towards performance and learning.
In particular, the TWP programme focuses on identifying specific behaviours that require attention, introducing the human-social factors that drive those behaviours and developing a plan for change. Coaching support is provided to generate confidence in applying new strategies.
The TWP programme will provide leaders with:
- improved communication skills
- an understanding of relevant human-social factors and strategies for their use
- a clear view of current and preferred organisational performance
- a plan for applying new skills and strategies
- on-going coaching to support and optimise the new techniques.
Typically a TWP programme would commence with a Workplace Review. The review provides Tima Consulting with an understanding of workplace culture and issues from the perspective of both employees and leaders.
esCollate Software
esCollate provides real-time data capture and feedback for
manufacturing, establishing a solid platform for streamlining processes and engaging factory employees.
The esCollate software is supported by a range of services that include a review of the work environment, training and coaching of front line managers, and the implementation of strategies that improve every day performance.
esCollate provides sophisticated factory modelling that includes analysis by machine, line, line area, route and factory area. Support for varying shift patterns and product details specific to each product-route combination allow complex operational activity to be accurately logged and reported.
esCollate supports lean manufacturing and continuous improvement initiatives with accurate, objective information. A full time presence on the factory floor keeps the focus of attention on key performance measures.
An implementation of esCollate delivers the following benefits to the organisation:
- accurate, objective data on plant performance including OEE
- cognitive engagement of factory employees and linking of factory floor teams
- support for structured communication between factory employees and front line management
- accelerated uptake of lean manufacturing and continuous improvement initiatives.
For more information please visit www.escollate.com
About Tima
We understand human-social factors and their application in driving behaviour change and improving organisational performance.
We improve individual, team and organisational performance through the effective application of human-social factors. Tima Consulting’s approach delivers cognitively engaged and intrinsically motivated employees, as well as work practices that lead to a performance and learning environment.
Tima Consulting’s focus is on practical techniques that drive meaningful and sustained change. Interventions typically span a medium to long term and involve several different reviews from Productivity & Performance, Operational Excellence and a Workplace Review. These Reviews are followed by a software implementation of esCollate and a Transformational Work Practices programme.
The services and software delivered by Tima Consulting are based on many years of manufacturing experience, observation and research. Tima Consulting has a proven track record of implementing positive change strategies which include the human and cultural aspects of organisational performance as well as process changes to improve productivity and overall performance of the company.
Tima Consulting was founded and developed by Sean Thomas. Sean had a long-term interest in motivation, particularly motivation in the workplace. He developed an understanding of the factors that drive human behaviour and what an organisation can do to ensure employees are optimally motivated and focused on appropriate outcomes. Sean had a passion for developing and mentoring people, developing new workshops and products.
Sadly, with Sean Thomas’ unwelcome and untimely illness and passing, Mark Edwards has taken over the business and is CEO and Director of Tima Consulting. The team at Tima Consulting still works with the same people focus that Sean had developed over the years.
Mark has 25 years senior management, initially 15 years in Commercial Banking and last 20 years in Contracting / Consultancy, including 13 years with Tima Consulting – 10 years in a Business Development and Strategy advisory role and more recently CEO.
Mark is a member of Institute of Finance Professionals NZ Inc (INFINZ) and NZ Qualified Bookkeepers Association (NZBQA) and has been a member of Institute of Directors (IOD). Mark has a Degree in BBS in Banking & Finance and holds a certificate in Company Direction from IOD.
Kim Hooper, People & Process – Process, Productivity & Performance, a veteran of 30 years working for the world’s largest FMCG companies at every level and across Petfood, Human food and Confectionery (chocolate) businesses, within the; supply chain, in Engineering, Operations Management, Technology and Factory Management. In later years moving into Senior Business Management teams, Regional & Global Supply Chain management, cross functional teams and global Brand boards.
More lately Kim has added value leading Factory Productivity transformations and turnarounds – Design & Deliver step changes in manufacturing performance in local and Trans-regional factory networks. In addition to productivity transformation Kim has assisted organisations with:
- Cross regional, root cause Investigations into major deviations in supply chain performance. Particularly relating to Engineering & Food safety.
- Reviewing & Sharpening Supply / Manufacturing strategy and deployment.
- Building/ Expanding large scale Food facilities across multiple countries and cultures.
Kim has Honours Degree, Bachelor of Technology Manufacturing from Massey University.
John Mullany, People & Process – Process, Productivity & Performance, with 30+ years working across three continents experiencing numerous cultures and varying levels of uneducated to highly educated work force. John brings an array of manufacturing experience (Business Process Improvement, Operational Excellence, Performance Support, Change Management and Project Management) that benefits client’s through a people focus that spans from day-to-day Production Process to Supply Chain for the FMCG and both Heavy & Light Manufacturing sectors. For the FMCG sector, John has worked with Chocolate, Dairy, Alcohol, Bottling and Milling & Blending manufacturers for such companies as; Cadbury’s, Clover Dairy, United Breweries and Freddy Hirsch Group. In the Heavy & Light Manufacturing sector for such companies as Boart Longyear, Powertech Transformers, Henkel Adhesives, Scaw Metals Group, Com Dev Electronics, Volkswagen and Lowe Corporation.
Saskia van der Geest, Process – has launched over a hundred products (and some businesses) onto the NZ market and with over 25 years of experience focusing on improving the new product development (NPD) process and over 20 years’ experience managing NPD projects in NZ.
Specialising in improving the NPD process to consistently deliver ‘faster, better, more profitable’. That is better quality new products (or services), in shorter time frames, with reduced cost, higher margins and reduced risk, thus improving product development productivity, lifting efficiency and
effectiveness.
Saskia has a Master’s degree in Industrial Design Engineering from Technische Universiteit Delft and a Marketing degree, has worked as a Marketing Manager, a Product Manager, and an Innovation Manager.
Angelika Barnes, People & Process – Leadership, with 25 years of operational process and people management coaching Angelika provides clients with valuable insights and a focus on solutions.
Jaime Brookes, People & Process – Design, has 17 years design experience with Tima Consulting. He is responsible for all UX design, visual design and marketing materials, as well as working closely with Product Development to facilitate software designs from idea to completion.
Tima Consulting has worked with the following companies to improve productivity:
CONTACT US
Thank you for your interest in Tima Consulting to improve individual, team and organisational performance. We look forward to hearing from you.
Mark Edwards – CEO
m | 027 483 3275
e | mark.edwards@tima.co.nz
Postal
Tima Consulting, PO Box 548, Nelson 7040, New Zealand.